
The result quickly became apparent: All signs of contamination from carbon and black specks were removed in the subsequently produced preforms, leading to a dramatic improvement in product quality. Their speed to market and preform development is one of their greatest attributes that allows us to quickly and effectively ramp up new projects. They have great technical knowledge, competitive pricing, and excellent service and quality on all preforms they supply. In order to find a suitable solution to readjust the client’s PET preform manufacturing process, Chem-Trend recommended to use the Ultra Purge™ purging compound technology during colour and tool change processes. EFI has been a great partner over the past several years. The solution: Ultra Purge™ purging compounds Subsequently, Chem-Trend’s technical experts determined a window for preventive purging during routine mould and product change that helped the customer to resolve the common, yet challenging issues of PET preform production. How Chem-Trend identified the problemĭuring a technical assessment, the team identified the extruder and shooting pot areas of the machine as the main sources for material degradation and carbonization, which resulted in black specks, and focused on finding out an opportune time for maintenance to take place without hindering production. Process Drying of the Pet (granules) Plasticization of PET Injection molding of the preform Heating the preform Blow molding of the preform Cooling and. Chem-Trend analyzed the situation together with the customer and figured out: a major obstacle to quality control was the packaging company’s short cycle times and high volume 24/7 preform production schedule limiting the chance for effective cleaning maintenance. The main issue the food packaging company had to face during the PET production process: Defective preforms needed to be identified and discarded before they made their way into bottles. Defective preforms result in customer complaints and batch rejections Chem-Trend set out to find a solution – and finally managed to solve the problem in close collaboration with the customer. Quality problems stemming from carbonization and colour change issues in the injection moulding process were not being detected prior to shipment.
PET PREFORM MANUFACTURING PROCESS SERIES
How was the manufacturer able to identify and solve the problems associated with carbonization and colour change – and why was the cooperation with Chem-Trend crucial?Ī food packaging company was experiencing a series of challenges in their manufacturing process of PET preforms.
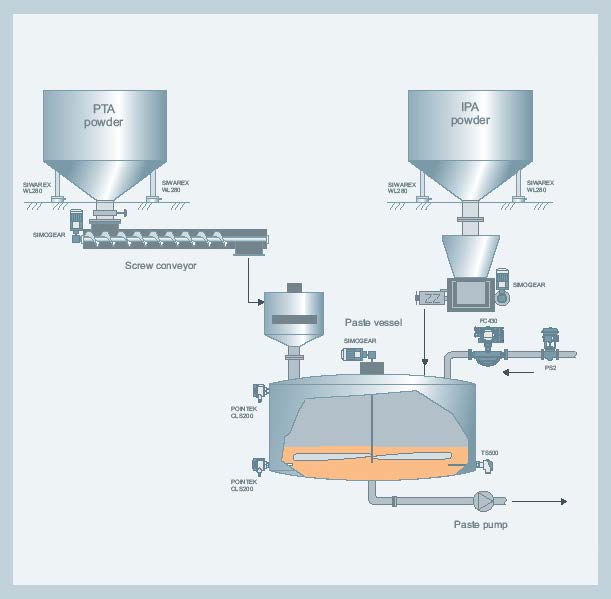
The following example of a food packaging company illustrates the issues involved. When compared to other systems in its category, H-PET AE delivers the lowest part cost and best energy efficiency.The production of PET preforms is based on a multi-stage moulding process. Husky's H-PET™ All-Electric (AE) system is an efficient, affordable solution for lower volume markets, offering exceptional value. HyPET HPP also features a unique sustainable option for Recycled Flake (RF). HyPET HPP provides preform lightweighting capabilities by enabling thinner-wall sections saving resin on every shot consistently for the life of the system. Husky's High Performance Package (HPP) allows you to take the productivity and efficiency of your HyPET system to the next level. This makes it possible to achieve the most stable process and reliable operation, which results in the fastest cycles and leading preform quality. All components of our HyPET system are specifically designed to work together as a fully integrated and optimized workcell. Husky HyPET™ systems are available in various tonnages for molds between two and 144 cavities. Husky also offers a diverse range of services, including preform prototyping, preform lightweighting, mold conversions and refurbishing. It's complex to list all the pet bottle preform machines here, I will take the 390Ton pet bottle injection moulding machine as an example to give you a clear comprehension about the 28mm 13g 64 cavities water bottle performs manufacturing. As a trusted partner, Husky takes responsibility for the complete workcell, overseeing configuration, supply and startup, as well as providing global support, service and parts. Our preform injection molding systems deliver the industry's lowest total production costs for the widest range of preforms and production volumes. A complete manufacturing solution from Husky minimizes overall investment risk and reduces total cost of ownership Husky has been the leader in the preform manufacturing equipment industry for over 35 years having more than 4,000 systems running in the field.Newer generation Husky systems maintain backwards compatibility.Integrated systems get up and running faster and keep running more efficiently.Easy to operate fully integrated workcells reduce variability in the injection molding process.

